Next Level Aerospace Profiling Explained
Aerodynamic Profiling Pdf Designed for components like compressor blades, vanes, fan blades, and turbine blades, our robotic profiling systems deliver exceptionally accurate elliptica. Canadian firm av&r aerospace needed to refine their precision application of robotic deburring of aerospace turbine blades. known as profiling, a precise edge is needed on the blades to control airflow while increasing efficiency and fuel economy in aircraft engines.
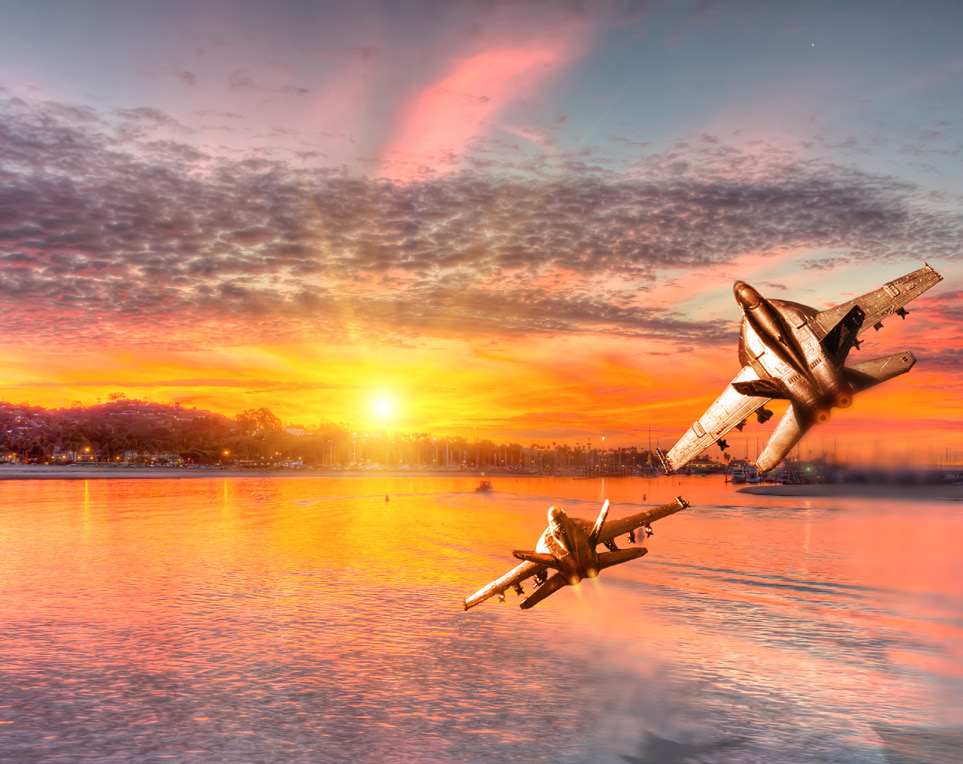
Elemental Depth Profiling Analysis For The Aerospace Defense Industry What is elemental depth profiling? elemental depth profiling is a chemical purity evaluation of a wide variety of solid samples such as multi layered films or coatings on metals and alloys, manufactured carbons or ceramics. This paper describes the data acquisition experiments that involved two laser beams propagating between an orbiting airborne platform and a stationary ground terminal over an 8 km slant path. Av&r aerospace’s automated profiling systems create high precision elliptical profiles on blades and vanes according to the engineers’ design. these 6 axis systems integrate adaptive and closed loop capabilities coupled with final leading and trailing edges profile inspection to reach a ± 37.5 micron tolerance (± 1.5 thousandth of an inch). Profiling aircraft frames involves the precise shaping and design of structural elements essential for aircraft integrity and performance. this process allows for optimized weight distribution, thereby enhancing fuel efficiency and reducing operational costs.

Nonwoven Machinery Texnology Av&r aerospace’s automated profiling systems create high precision elliptical profiles on blades and vanes according to the engineers’ design. these 6 axis systems integrate adaptive and closed loop capabilities coupled with final leading and trailing edges profile inspection to reach a ± 37.5 micron tolerance (± 1.5 thousandth of an inch). Profiling aircraft frames involves the precise shaping and design of structural elements essential for aircraft integrity and performance. this process allows for optimized weight distribution, thereby enhancing fuel efficiency and reducing operational costs. Aerodynamic profiling techniques encompass methods designed to analyze and enhance the airflow around an object, particularly aircraft. these techniques assess how air interacts with surfaces, ultimately affecting performance and efficiency in flight. Aerodynamic profiling entails the systematic design and analysis of the airflow around objects, particularly focusing on minimizing drag and maximizing lift. in the context of turbine engines, this process is vital for ensuring optimal performance and operational efficiency. Understanding next higher assembly (nha) in aviation, an nha refers to a fully assembled unit that consists of multiple sub components or parts. these sub components are interconnected and work together to perform a specific function within the aircraft. Key trends (high precision mems for aerospace applications market ) miniaturization & weight reduction: increasing demand for lightweight, compact mems sensors to enhance aircraft fuel efficiency. advancements in mems sensor fusion: integration of multiple mems sensors for real time data processing and improved accuracy.

Career Pathways For Aerospace Systems Engineers From Entry Level To Aerodynamic profiling techniques encompass methods designed to analyze and enhance the airflow around an object, particularly aircraft. these techniques assess how air interacts with surfaces, ultimately affecting performance and efficiency in flight. Aerodynamic profiling entails the systematic design and analysis of the airflow around objects, particularly focusing on minimizing drag and maximizing lift. in the context of turbine engines, this process is vital for ensuring optimal performance and operational efficiency. Understanding next higher assembly (nha) in aviation, an nha refers to a fully assembled unit that consists of multiple sub components or parts. these sub components are interconnected and work together to perform a specific function within the aircraft. Key trends (high precision mems for aerospace applications market ) miniaturization & weight reduction: increasing demand for lightweight, compact mems sensors to enhance aircraft fuel efficiency. advancements in mems sensor fusion: integration of multiple mems sensors for real time data processing and improved accuracy.
Comments are closed.