Mig Vs Tig Welding Types Materials And Applications A Guide
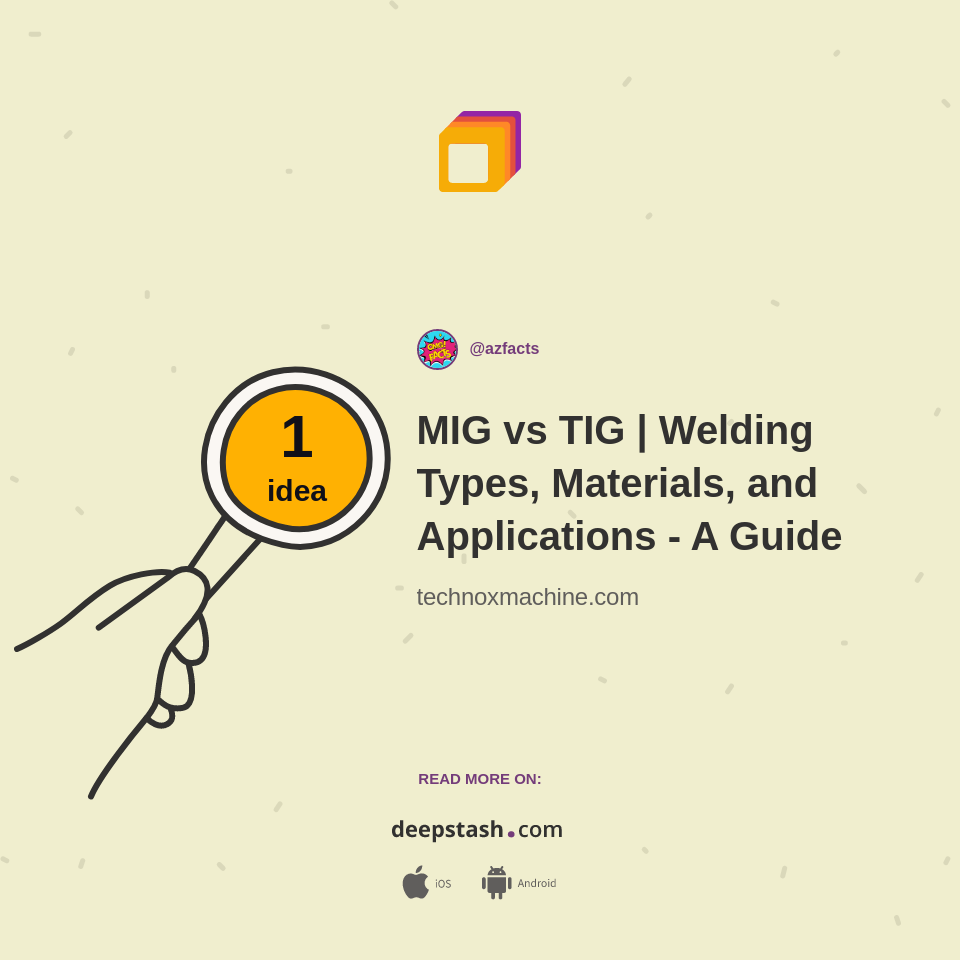
Mig Vs Tig Welding Types Materials And Applications A Guide Though both utilize an inert shielding gas and externally supplied filler material to join base metals, mig and tig welding differ in key application areas such as workpiece thickness capabilities, quality of welds produced, and operator skill requirements. Discover the differences between mig and tig welding techniques, explore various types, suitable materials, and applications. get expert insights on choosing the right welding method for your project.
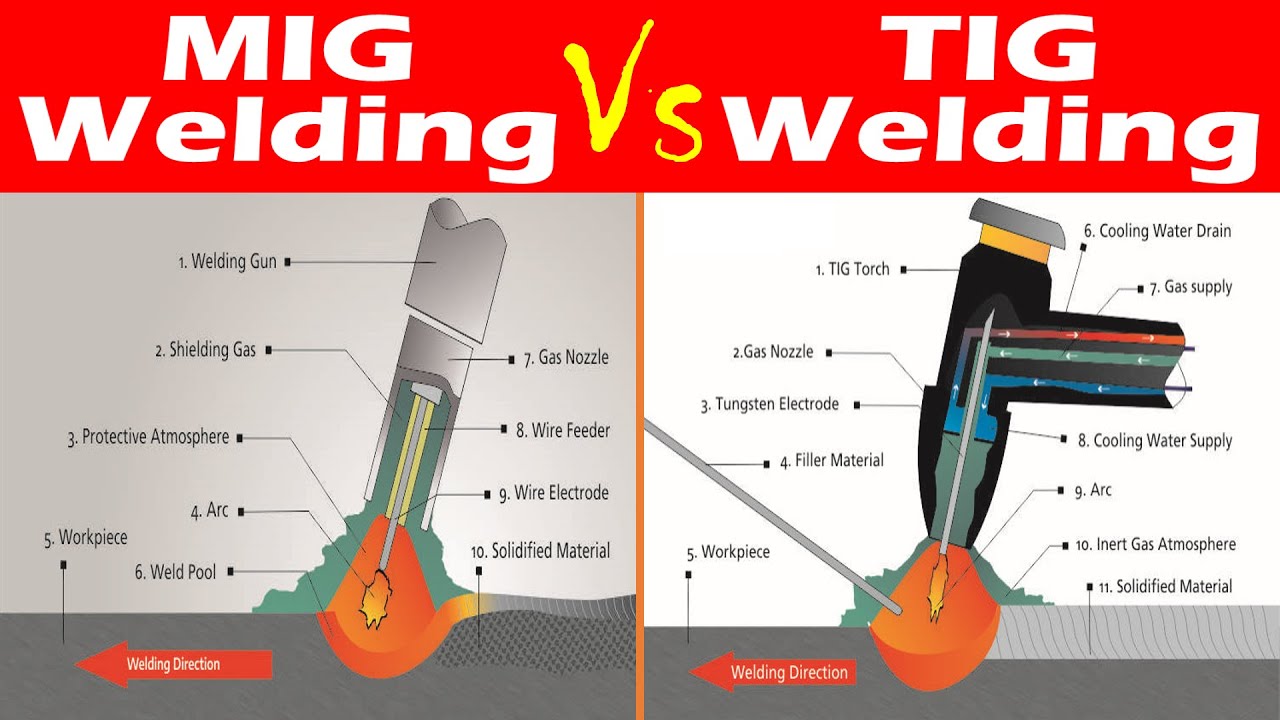
Mig Vs Tig Welding Types Materials And Applications A 54 Off In this guide, we’ll break down everything you need to know about mig vs tig welding, including their differences, strengths, limitations, and the types of materials and applications they’re best suited for. Mig vs tig welding: compare processes, pros, cons, materials, and applications to choose the best welding method for your specific project needs. Both mig and tig welding are arc welding techniques that use an electric arc to generate heat for joining metals. however, their approaches, equipment, and applications differ significantly, making each method better suited for specific scenarios. Learn the main differences between mig and tig welding, including their speed, material compatibility, precision, and ideal use cases. discover why mig welding is great for faster, thicker material projects, and tig welding excels in precision work for thinner metals.
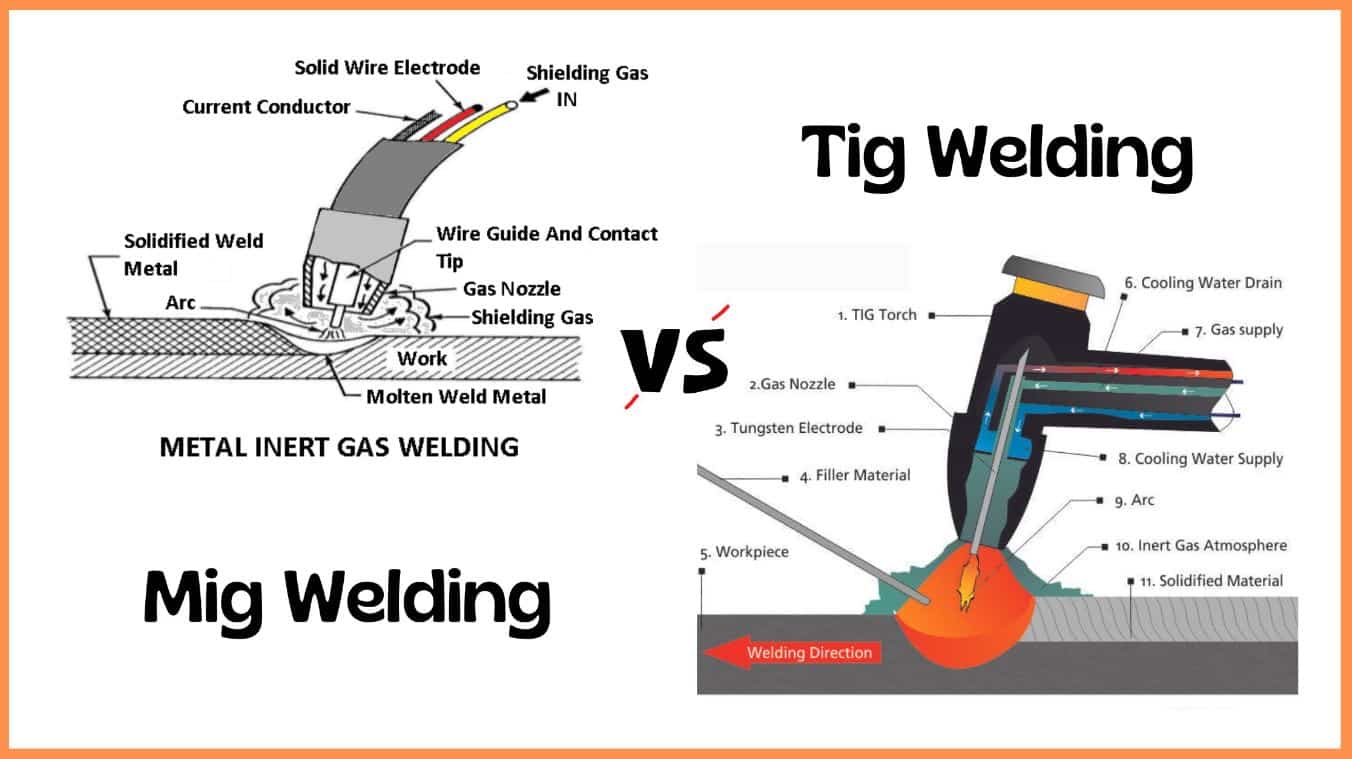
Mig Vs Tig Welding Types Materials And Applications A 44 Off Both mig and tig welding are arc welding techniques that use an electric arc to generate heat for joining metals. however, their approaches, equipment, and applications differ significantly, making each method better suited for specific scenarios. Learn the main differences between mig and tig welding, including their speed, material compatibility, precision, and ideal use cases. discover why mig welding is great for faster, thicker material projects, and tig welding excels in precision work for thinner metals. This comprehensive guide will delve deep into the intricacies of both mig and tig welding, comparing their working principles, advantages, limitations, and best applications. The main difference between mig and tig welding is the electrode they use to create the arc. mig uses a consumable solid wire that is machine fed to the weld, whereas tig welding uses a non consumable electrode. Table of contents: 2.1. mig welding. 2.2. tig welding. 3.1. electrode type. 3.2. shielding gas. 3.3. welding speed and efficiency. 3.4. heat input and control. 3.5. material compatibility. 3.6. skill level and learning curve. 4.1. material thickness and type. 4.2. production and speed. 4.3. specific industries and projects. 5.1. mig welding. 6.1. The difference between tig (tungsten inert gas) and mig (metal inert gas) welding is that tig welding uses a tungsten metal rod to fuse two metals directly together, while mig welding uses a feed wire through a spool gun to weld two metals together.
Comments are closed.