Ansys Fluent Tutorial Flow In A Pipe With Multiple Inlet 59 Off
Ansys Fluent Tutorial Part 2 Overview Pdf Turbulence Classical The velocity and temperature are different in each inlet, find the equivalent velocity and temperature at the outlet. what would you learn from this tutorial?. Once you have the geometry of the fluid part, in ansys meshing you can set the names of the boundaries by creating named selections. if you decide to use fluent meshing, then you can do the same by creating groups in spaceclaim.
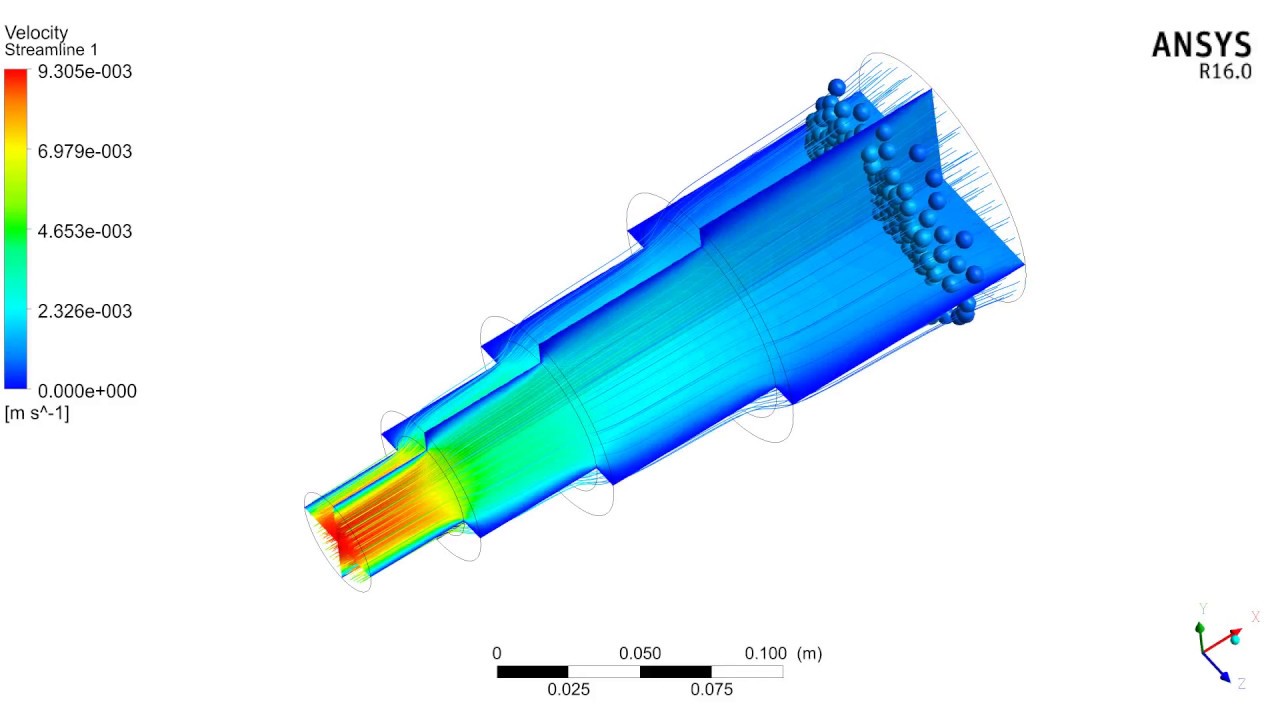
Ansys Fluent Tutorial Flow In A Pipe With Multiple Inlet 59 Off The following example shows you how to setup to use dot(), vector(), moment(), and force() expression operations in ansys fluent. six expressions are defined: aoa, dragforce, flowdir, liftforce, moment, and totalforce. The velocity and temperature are different in each inlet, find the equivalent velocity and temperature at the outlet. what would you learn from this tutorial? application of revolve, edge blend application of extrude from face option. non conformal meshing in ansys. This tutorial demonstrates how to simulate fluid flow in a pipe using ansys fluent. the key steps include: 1) reading an existing mesh file of a half pipe geometry and verifying the grid dimensions. 2) defining water as the fluid material and setting inlet, outlet, and fluid boundary conditions. In this video, i will demonstrate the flow situations that usually happens when a fluid enters a pipe with certain inlet velocity.
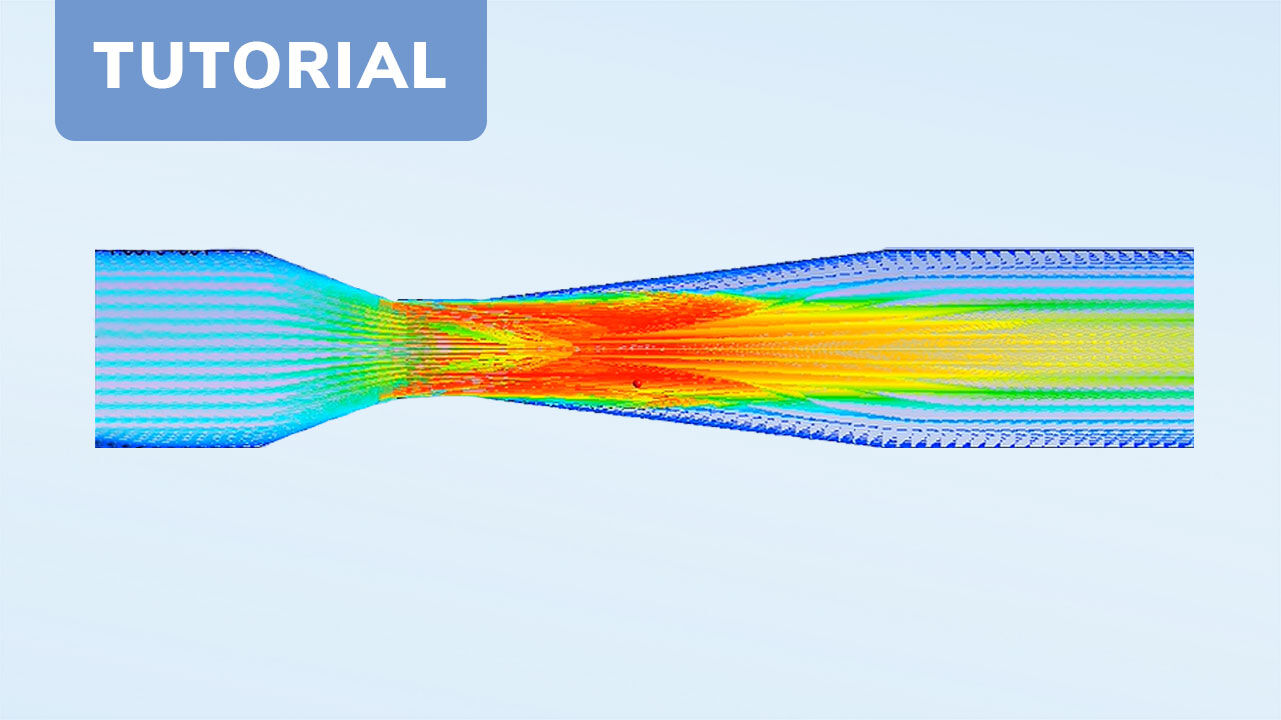
Ansys Fluent Tutorial Flow In A Pipe With Multiple Inlet 59 Off This tutorial demonstrates how to simulate fluid flow in a pipe using ansys fluent. the key steps include: 1) reading an existing mesh file of a half pipe geometry and verifying the grid dimensions. 2) defining water as the fluid material and setting inlet, outlet, and fluid boundary conditions. In this video, i will demonstrate the flow situations that usually happens when a fluid enters a pipe with certain inlet velocity. However i'm having a issue with setting up the compressor boundary conditions, i am currently using a pressure outlet with a target mass flow but get reverse flow during convergence and the simulation only tends to converge to 10^ 3 before repeating. 1. fluid flow in an exhaust manifold 2. fluent postprocessing : exhaust manifold 2.4.9. creating a scene with multiple graphics features 2.4.11. animating the display of results in successive streamwise planes 3. modeling flow through porous media 4. modeling external compressible flow 5. fluid flow and heat transfer in a mixing elbow 6. exhaust system: fault tolerant meshing 7. modeling. The flow of fluids in a pipe is widely studied fluid mechanics problem. the correlations for entry length and pressure drop are available in terms of flow reynolds number. this tutorial demonstrates how to do the following: • read an existing mesh file in fluent. • verify the grid for dimensions and quality. In this video you'll understand, how to solve simple flow problem in ansys fluentwelcome to our channel, "sampurna engineering". we create lecture videos for.

Ansys Fluent Tutorial Flow In A Pipe With Multiple Inlet Ansys However i'm having a issue with setting up the compressor boundary conditions, i am currently using a pressure outlet with a target mass flow but get reverse flow during convergence and the simulation only tends to converge to 10^ 3 before repeating. 1. fluid flow in an exhaust manifold 2. fluent postprocessing : exhaust manifold 2.4.9. creating a scene with multiple graphics features 2.4.11. animating the display of results in successive streamwise planes 3. modeling flow through porous media 4. modeling external compressible flow 5. fluid flow and heat transfer in a mixing elbow 6. exhaust system: fault tolerant meshing 7. modeling. The flow of fluids in a pipe is widely studied fluid mechanics problem. the correlations for entry length and pressure drop are available in terms of flow reynolds number. this tutorial demonstrates how to do the following: • read an existing mesh file in fluent. • verify the grid for dimensions and quality. In this video you'll understand, how to solve simple flow problem in ansys fluentwelcome to our channel, "sampurna engineering". we create lecture videos for.
Comments are closed.